What is Galvanized Steel? Uses, Benefits, and Processes
February 26, 2025 | Categorized in: Types
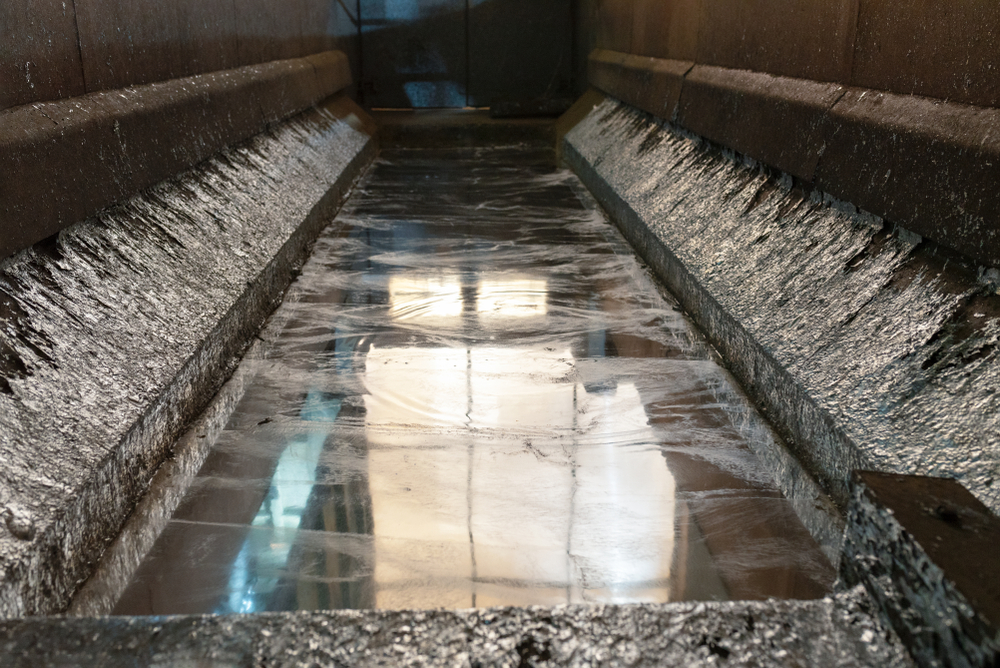
Simply put, galvanized steel is steel that has had a zinc coating applied on top of the original metal. Unlike stainless steel, which changes the chemical composition of steel (by adding chromium), the coating is made of zinc that in turn forms a barrier between the steel and moisture in the air, effectively sealing it from elements that can lead to rusting.
The zinc layer is softer and essentially “sacrifices” itself to protect the metal inside from scratches, corrosion, and more. Galvanized steel also has a very identifiable “spangled” pattern with small lighter and darker spots.
Does galvanized steel rust? (And other benefits)
When choosing building materials for a project, there are a lot of factors to consider. For environments where metal needs to be resistant to rusting and corrosion, such as outdoors, steel is a great candidate. However, not all steel is rust-resistant. Stainless steel and galvanized steel are both types of steel that are used for their ability to withstand rusting and corrosion.
As already mentioned above, galvanized steel’s primary benefit is its rust and corrosion resistance. In addition to that, galvanized steel also lasts a long time (an estimated 80+ years in an average environment and 50 years in an environment with high exposure to water or corrosive soil) and requires little to no maintenance.
Beyond keeping costs low during its lifetime, galvanized steel also has low upfront costs compared to other treated metals and other options for rust resistance. Even more, the process — which we’ll discuss below — is very quick and can be completed start-to-finish in half a day.
Click here for more information on the galvanizing services that we provide.
What is galvanized steel used for?
Because the benefits of galvanization are so valuable and applicable to so much of steel’s uses, there are almost limitless applications for it. From items as small as nuts and bolts that need to withstand outdoor weather conditions to bike frames, ladders, car bodies, and exposed steel structures or frames, galvanized steel helps to extend the lifetime and minimize the required maintenance.
The use of galvanized steel has become very common, particularly in the infrastructure, agriculture, automotive, and construction industries, which need to have reliable materials that can last decades in all kinds of weather and outdoor conditions.
How to galvanize steel
Now that we understand why galvanized steel is useful for a wide variety of applications, we need to understand how it’s done. The two primary methods for galvanizing steel are hot-dip galvanization and electrogalvanization.
1. Hot-dip galvanization
The more common of the two techniques, hot-dip galvanization (as the name suggests) involves dipping the piece of metal into molten zinc to form a protective layer on the surface. Below is a video from the American Galvanizers Association (AGA) that demonstrates the process:
Before that can be done, however, the steel has to be prepared. It’s usually cleaned with a degreasing solution prior to being pickled in diluted sulfuric acid. It’s then fluxed to make sure the surface is clean before dipping into the molten zinc vat. The final step is to let the steel cool and inspect it to ensure the zinc coating is evenly applied and doesn’t have any damage.
2. Electrogalvanization (a.k.a zinc plating)
In certain applications, such as steel used for car bodies, galvanizing is required, but the thick layer provided by the hot-dip method causes issues with paint adhesion. Instead, they use electrogalvanization (also referred to as electroplating or zinc plating) to achieve corrosion resistance but with a thinner coat of zinc.
The process involves a mixture of saline and zinc rather than molten zinc, which the metal (in this case, car body) is dipped into. An electrical current is then run through the tank and mixture, causing the zinc to be bonded to the steel’s surface and form the protective galvanized layer.
Watch the video below to learn more about the galvanization process:
Unfortunately, as many people living in cold or coastal environments, such as Houston, can tell you, this doesn’t prevent rust and corrosion as effectively, or for as long as hot-dip galvanization.
Process differences
When we compare hot-dip galvanization and zinc plating, we can see some immediate differences jump out:
Process |
Hot-Dip Galvanization |
Electrogalvanization (Zinc Plating) |
Coating Thickness |
Thicker coating, offers superior corrosion resistance |
Thinner coating, suitable for lower-corrosion environments |
Durability |
Often lasts up to or beyond 100 years in outdoor environments |
Lasts several decades but less durable than hot-dip |
Size Limitations |
Suitable for small to very large components |
Best for smaller components |
Paint Adhesion |
Paint may not adhere as well |
Provides a smoother surface, ideal for painting |
Application |
Used for structural steel, outdoor components, and heavy-duty equipment |
Used for precision parts and components requiring uniform coating |
Ideal Environment |
Outdoor, harsh conditions, minimal maintenance |
Indoor or low-corrosion environments |
As mentioned, hot-dip galvanization results in a much thicker protective coat, which provides better corrosion resistance than electrogalvanization if paint adhesion isn’t a concern. Another difference is that electrogalvanization typically needs to be limited to smaller components, while hot-dip galvanization can be used for all sizes.
While electroplating lasts several decades, it doesn’t last as long as hot-dip galvanized coatings, which often last up to (and sometimes beyond) 100 years. To summarize, electrogalvanization is ideal for smaller components where a precise, uniform coat is important and high levels of corrosiveness won’t be encountered. Hot-dip galvanization is ideal for larger pieces that are outdoors or will face harsh conditions for decades to come, and minimal maintenance is important.
Galvanizing steel vs. powder coating
Another process sometimes used for improving steel’s corrosion resistance is called powder coating. It involves a piece of steel being sprayed with dry powder made from pigment and resin, which sticks to the steel by charged static electricity. This is then put in a curing oven to melt and cool, creating a protective layer over the steel. Comparing the two methods, there are quite a few differences:
Galvanizing |
Powder Coating |
|
Coating Thickness |
Thicker, provides superior corrosion resistance |
Thinner, offers less effective corrosion resistance |
Lifespan |
Nearly 100 years with minimal maintenance |
15–20 years with ongoing maintenance |
Durability |
Highly durable, withstands harsh environments |
Less durable, prone to wear and chipping over time |
Cost |
Cost-effective over the lifetime of the product |
Higher initial cost and maintenance expenses |
Ideal Environment |
Outdoor, heavy-duty, long-term applications |
Aesthetic or light-duty indoor/outdoor applications |
As outlined above, hot-dip galvanizing not only lasts for much longer (nearly 100 years with no maintenance vs. 15-20 years with some maintenance), but also has a thicker and more effective coat that can be cheaper over its lifetime.
While powder coating initially had a reputation for being cheaper than traditional galvanizing, it has since drastically risen in price and material costs have more than doubled. This, coupled with necessary and continual upkeep like cleaning (albeit not a huge expense), can add up to a significantly more costly product with worse durability and a shorter lifespan.
Galvanized steel vs. stainless steel
We mentioned that stainless steel can also be used for resistance to corrosion and rust, but not all of galvanized steel’s benefits carry over to stainless steel. For instance, the price stainless steel is much more expensive than the cost of galvanizing services for steel products.
The drastically higher price is a factor of the added chromium to the alloy, which also makes the steel stronger and more corrosion resistant than simply galvanizing. This is useful for very extreme environments, but for the majority of land-based and more common applications, galvanized steel will be the better choice simply because of the cost — both initial and for upkeep.
Galvanized steel – FAQs
How strong is galvanized steel?
Galvanized steel’s strength is comparable to the base steel used. The zinc coating primarily adds corrosion resistance without significantly affecting its structural integrity, making it ideal for applications requiring durability and longevity.
Can you paint galvanized steel?
Yes, you can paint galvanized steel, but it takes a little prep work. Clean it well and use a primer made for galvanized surfaces. This ensures the paint sticks and gives extra protection while adding a polished look.
Can you weld galvanized steel?
Yes, you can weld steel that has been galvanized, but safety is key. The zinc coating produces fumes when heated, so work in a well-ventilated area and wear proper gear. After welding, you’ll need to reapply protection to prevent rust in those spots.
Is galvanized steel magnetic?
Yes, galvanized steel is magnetic because it retains the magnetic properties of its base steel. The zinc coating does not interfere with magnetism, making it suitable for applications requiring magnetic properties.
How long does galvanized steel last?
The lifespan of galvanized steel depends on its environment. In dry, indoor conditions, it can last up to 100 years. Outdoors, especially in salty or humid areas, it might last 50-80 years before significant corrosion occurs. Regular maintenance extends its life.
Reach out to get a free quote on galvanized steel!
Galvanized steel is invaluable to projects around the globe because of its characteristics, ease of production, and cost-effectiveness. Across a wide range of industries and applications, it is relied on to be dependable and have unparalleled longevity. If you’re looking to get this same durable protection for your projects, get in touch with our team of experts or request a quote for galvanized steel today.