GUIDE TO STEEL HEAT TREATING
September 16, 2021 | Categorized in: Production
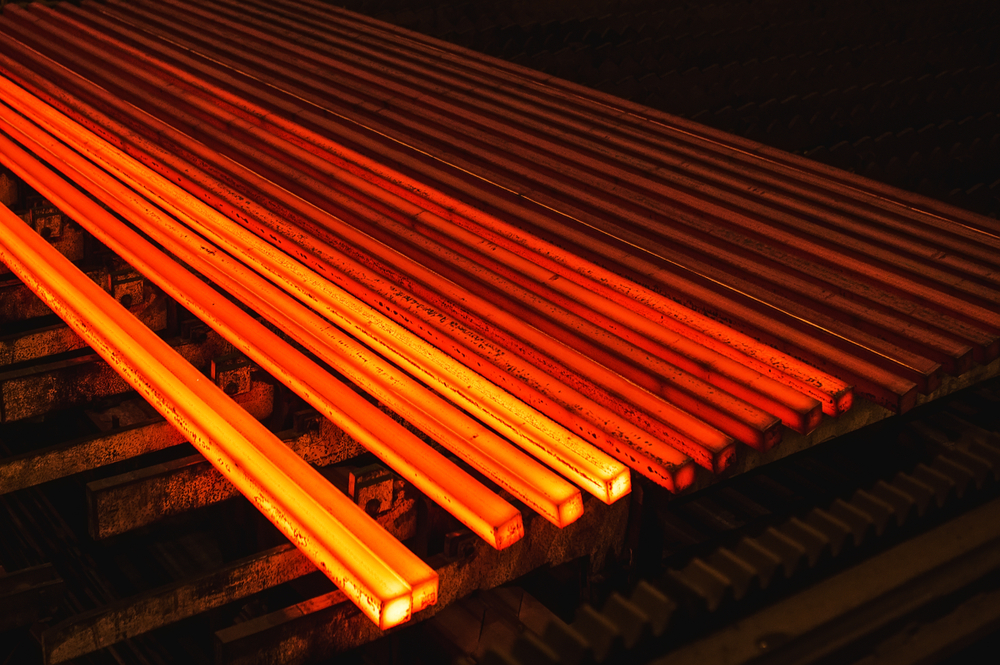
Red hot metal isn’t an uncommon sight in steel manufacturing, but did you know that it’s not just the forging process you might be looking at? Heat treating is an important part of most builds involving steel (particularly those using steel for structural purposes). But why does reheating steel make any difference, let alone such a difference that it’s integral to many projects? Keep reading to learn more.
What is heat treating?
During World War 2, heat treatment of steel saw a huge increase in focus and funding as mass manufacturing facilities opened across the country to fuel the war effort. The discovery of the additional strength heat treating provided wasn’t the only finding that was made during this time, however. Ships that were made from heat-treated steel sometimes fractured at weak points when exposed to cold Atlantic waters.
This is because as steel (and all metals) increases in hardness, it also increases in brittleness. Due to this tradeoff, different heat treatment methods of steel were developed to maximize strength without sacrificing resistance to fracturing. However, before we discuss the specific methods, we need to understand the basic steps of the heat treatment process.
Heat treating stages
While there are differences between specific methods that will be talked about in their sections, the general steps of heat treating are the same across all of them. Heat treating broadly consists of the heating, soaking, and cooling stages to change the metallurgical structure into a stronger, more uniform one without impurities.
Heating
During the heating stage, the metal is heated uniformly without letting it reach its melting point. This is done slowly to ensure heating is even and one section of the metal doesn’t expand more than another, which would lead to cracked or weakened sections. How quickly you can heat the metal without damaging it will depend on factors such as the condition and history of the steel as well as the size, type, and grade.
Soaking
Once the steel has been heated to the desired temperature at the specified rate, it’s held at that temperature for a certain period of time. This duration also depends on factors of the steel from the previous section, in addition to the desired properties of the final product. The reason for holding the metal at this higher temperature is to allow the structure time to change to the desired configuration and shape. Because this step affects the properties of the atomic and chemical structure of the steel, those factors will also be crucial to determining the correct soaking time. As you can imagine when it comes to the atomic structure of a material, precision is vital in this step especially.
Cooling
Once the steel has been soaked, it’s time to cool. There are many variations of this step (which we will discuss next), where it might involve quenching in a medium like water or oil, or it could simply involve allowing the metal cool in the air. Generally, water or brine are quicker at cooling than oil, which is quicker than air. How quickly the steel should be cooled will again depend on the type of steel (i.e. water used for carbon steels vs. oil used for alloy steels) as well as the desired final characteristics. Faster cooling methods like water quenching result in harder but more brittle steel, while slower cooling methods like air-cooling result in more ductile and tougher steel.
Types of heat treating
Now that we understand the basic process for heat treating, let’s take a look at the differences in methods:
Annealing
While most people think of heat treating as hardening a metal, annealing is actually a form of heat treatment that softens the material. This is done for the purpose of relieving stress or improving the grain structures (crystalline configuration) in the metal. Annealing is also one of the heat treatment methods that uses a slow cooling stage, usually either by letting the steel sit and cool in the furnace or by burying it in an insulating material.
Normalizing
The primary goal of normalizing is to remove internal stresses in the steel, similar to annealing. However, the key differences between the two are that normalizing is only done to ferrous metals (like steel) and the metal is removed from the furnace for air-cooling. Because this means that the cooling stage is quicker (room temperature air vs. furnace air), normalized steel becomes harder than annealed steel.
Hardening
As mentioned in the previous section, faster cooling usually results in harder steel. This method is usually done with a very quick temperature reduction (around 1 second), such as quenching the steel in water or brine. Unfortunately, this fast cooling increases the chances of warping or cracking during the extreme change, as well as increasing the metal’s brittleness once finished. After hardening, the steel’s strength is often higher than needed and is outweighed by the risk of breaking. One way to make the steel more malleable and less likely to shatter is by tempering.
Tempering
Tempering the steel is done after a quench and essentially repeats the heat treating process at a lower temperature. The steel is heated back up to another specified temperature that isn’t as high as its hardening temperature and allowed to soak, then set aside to cool in the air. This less extreme heating and cooling reduces the steel’s ductility and strength to a safer and more reliable level. For more information on the subtypes of tempering and steel colors at different temperatures, see our full resource on tempering.
Case hardening
The final major method of heat treating is called case hardening (or surface hardening), where only the outer layer of the steel is hardened. This is useful when a key consideration of materials is surface durability but the steel still needs to be able to absorb an impact or deformation without breaking. By having a softer core, case-hardened metals can achieve this.
The two major techniques for case hardening steel are carburizing and gas nitriding. Carburizing involves exposing the hot steel to carbon, which infuses the surface and strengthens it. Gas nitriding, on the other hand, exposes the hot steel to nitrogen or ammonia gas that reacts with the material to harden the surface.
Get your steel heat treated today
Heat treating your steel is a great way to improve the properties of the material and optimize it for certain projects and applications. It can not only strengthen beams, channels, and more, but can give you immense control over the characteristics that the steel brings to your project. Whether you’re looking for steel with a toughened surface to prevent scratches or cosmetic damage, or need to increase the ductility of your steel to reduce the chance of them fracturing, heat treating is exactly what you need. If you’re interested in buying steel, get in touch and request a quote or call one of our experts today.