Electric Arc Furnaces vs. Traditional Blast Furnaces
September 8, 2022 | Categorized in: Production
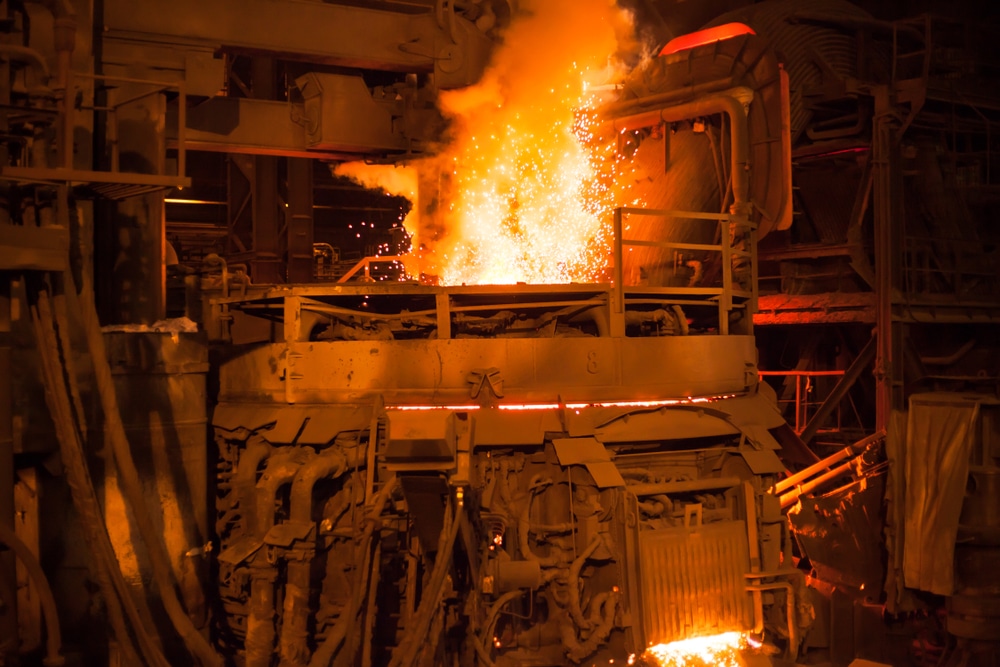
Steel manufacturing has come a long way since its inception. In a previous resource, we discussed the history of steel itself and how it has changed over time. A large reason why steel has changed is the techniques and technology surrounding its manufacturing. Today, we’ll take a closer look at a modern invention that has been revolutionizing how we produce, recycle, and reuse the most widely-used metal on the planet.
Basics of a furnace
The first step is understanding what a furnace is and what its purpose in the steelmaking process is. These are used to not only melt down steel, but also to remove the unwanted material that degrades the quality of the metal. This process of melting can either be used to initially remove the metal from raw ore, or to melt down existing metal to reform and reuse it. As you can see, furnaces are critical not only at the beginning of a metal’s “life,” but also each time it’s repurposed. Because the goal of a metallurgical furnace is to heat and melt metal, there are a number of different ways to achieve this. The two primary methods of supplying this heat are by using a blast furnace or using an electric arc furnace.
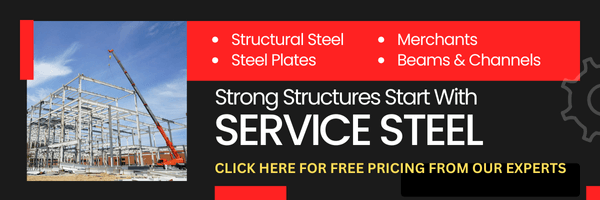
What is a blast furnace?
The older and more traditional of the two, blast furnaces can be traced as far back as ancient China (on a smaller scale). Modern blast furnaces use coke, or purified coal, to melt iron ore and create pig iron. Oxygen is then injected into the furnace, to reduce the carbon content of the steel and remove impurities. Blast furnaces take up a lot of room and produce a lot of carbon dioxide, but are easier to make clean steel with.
What is an electric arc furnace?
Electric arc furnaces, or EAFs, are a much newer incarnation of the metallurgical furnace and (as their name suggests) are powered by electricity. EAFs melt scrap and recycled metal by passing an electric current through graphite (or sometimes carbon) electrodes, creating an arc. This arc gives off huge amounts of heat, which melts the contents of the furnace. EAFs not only manufacture products quickly, but also typically have a relatively low initial cost.
Primary differences
While the end product from each of these is comparable, there are clearly differences between their capabilities and process. Comparing each type of furnace, the major distinctions are:
- Material source – blast furnaces can melt raw iron ore as well as recycled metal, while electric arc furnaces only melt recycled or scrap metal.
- Power supply – blast furnaces primarily use coke to supply the energy needed to heat up the metal, while EAFs use electricity to accomplish this.
- Environmental impact – because of the fuels used for each, EAFs can produce up to 85% less carbon dioxide than blast furnaces.
- Cost – EAFs cost less than blast furnaces and take up less space in a factory.
- Efficiency – EAFs also reach higher temperatures much faster and can melt and produce products more quickly, as well as having more precise control over the temperature compared to blast furnaces.
Environmental implications of EAFs
Steel is one of the most recycled materials on the planet and is actually considered 100% recyclable. And, as noted above, electric arc furnaces allow for a much cleaner way to produce it. Traditionally, fossil fuels like coal were used to power these massive furnaces — but now, technology has allowed us to produce this vital material in a more sustainable way, that aligns with the product’s environmentally-friendly characteristics.
Get strong steel for your projects today
If you’re ready to start building your projects, get in touch with Service Steel today! We have a huge inventory of structural steel and steel piling for a wide range of industries and undertakings. Talk to one of our experts or request a free quote today.
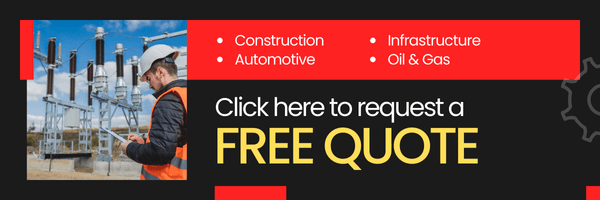