How is Sheet Metal Made?
July 9, 2021 | Categorized in: Types
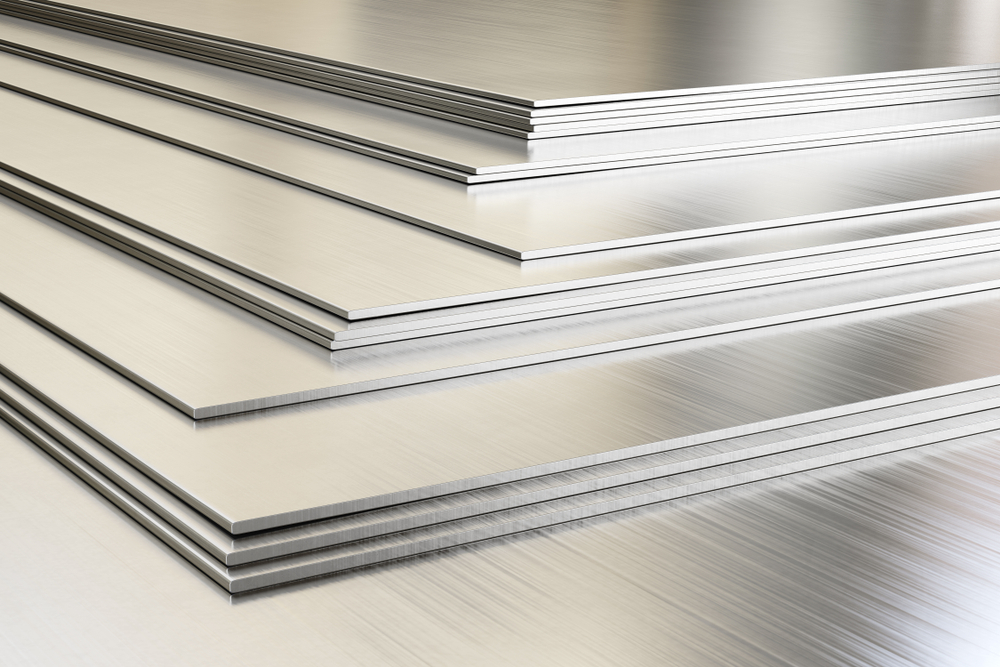
Whether you realize it or not, sheet metal is everywhere. From car bodies to roofs for buildings, plane wings to medical tables, and much more, sheet metal is a critical aspect of almost everything we do. Because of this, it pays to understand what exactly it is, where it comes from, and how it’s used.
What is sheet metal?
Sheet metal can often be used as a term to vaguely describe a category of metals that can be difficult to actually define. Generally, the criteria for being considered sheet metal is between 0.018” and 0.250” thick. However, inches or centimeters are not the primary measurement of a metal sheet’s thickness. It’s usually sorted by gauges, which can be converted into a specific thickness. Another variable of sheet metal is the material it can be made from, including aluminum, bronze, copper, brass, and a variety of types of steel.
Steel sheet metal manufacturing process
Because sheet metal is a relatively basic and straightforward product, with most variations coming from the gauge (thickness) and material, the general process for making it is also straightforward. The 4 primary steps are the melting of your chosen material, pouring it into a rectangular mold, pickling (removing impurities), and rolling and annealing the metal into a sheet.
1. Melting
The first step, unsurprisingly, is to melt the material for the sheet metal (commonly steel or aluminum) down until it’s molten. This is done so that the metal can be worked and processed easier and be pressed into a sheet. The temperature and time this takes will depend on the material, but the end product of molten metal is the same.
2. Pouring
Once the metal is completely liquified, it has to stay in that state as it’s poured into a rectangular mold. If it cools off, it will begin to harden in the wrong shape and will be much more difficult to process further. The rectangular mold gives it the general form it needs before the next steps of refining to thin it out and reach the desired shape and dimensions.
3. Pickling
After cooling in the mold and hardening into an ingot, the metal needs to be pickled. Similar to cucumbers sitting in a brine, the new metal piece will be submerged in a chemical mixture to remove impurities such as rust, scale, stains, and inorganic contaminants. This mixture can change depending on the application but usually involves a strong acid (such as hydrochloric or sulfuric acid) with additives for reducing corrosion and other properties.
4. Rolling & annealing
Now that the metal bar has cooled and been cleaned, it can be pressed into a sheet. The ingot is put through a pair of rollers that are moved closer to each other each time it goes through. This thins out the metal more and more as the metal is rolled several times, but as it gets thinner it also gets harder.
To continue rolling as the metal gets harder, annealing can be used. Annealing is heating the metal up again (not melting) and pickling it before running it through the rollers. By softening the metal again with annealing, it allows more processing to thin out the metal into a sheet that fits the desired specifications.
Why steel sheet metal is so common
Now that you know how sheet metal is made, you might be able to see why it’s so common. It’s a relatively basic manufacturing process that produces an adaptable product that can be different materials, have different characteristics, and therefore a variety of uses. Sheet metal also has a low weight to thickness ratio, making it easy to transport and work with. All of these benefits of the category make it popular across a wide range of industries and applications.